During many construction projects, there are several types of third-party inspections that are required by townships and building departments in order to receive final approval. One of these types of inspections is structural welding. Structural welding inspections are visual inspections in which welds are checked for a variety of factors for quality assurance to ensure the structures’ safety.
What is Welding? What Does a Weld Do?
The welding process helps fuse together materials like metal and steel using heat and pressure. This process should always be done by a certified professional welder that has the right experience and skill set. The job of a welder is to melt parts together, applying a durable filler material, and allowing these to cool resulting in a durable and strong bond. When done correctly, this process results in a strong and sturdy connection of 2 separate parts of construction with a spotless seam. Welding in construction is used to connect beams, trusses, columns, and footers to support walls, roof, and floors of a building; that makes welding a critical part of the construction process and having them done correctly is essential to the structural integrity and life-length of any construction project. A weld must be strong enough for its proposed use and any deficiency can weaken that weld below an acceptable level.
What Happens During a Welding Inspection?
A welding inspection must be done by a third-party certified welding inspector. These inspections are typically done in 3 phases: before, during, and after welding. Before welding, an inspector will look at the design plans and make sure that welds are being done at specified locations, under any specific conditions, and using materials requested by the designer on record. They will also ask to see the welder’s license to verify that they are certified and able to complete the job. Lastly, inspectors will check that the surface is clean of any rust, oils, dirt, paint, and any other contaminant that can affect the quality of the weld. During the welding process, an inspector will ensure that all specifications such as wire fire speed, voltage, technique and more are being followed by the welder. After the weld has been completed and cooled, an inspector will look for a weld that is smooth, uniform, and consistent in appearance. If during any of these phases the inspector notices a nonconformance, they will let the welder know how to correct it to certify quality work. For project owners, this saves time and money during construction and guarantees approval by townships or building departments.
Why Do Welds Weaken?
A weld can fail or weaken prematurely for a couple of reasons. Before the start of welding, impurities should be completely removed to guarantee the quality of the weld. Any contaminant that is not removed will become part of the weld and result in a weak weld that will fail. Signs that welds have been contaminated include bumps or holes where the contaminants are present. During the welding process, the right heating and cooling techniques need to be employed. If they aren’t, the bond will not be strong which will lead to the weld cracking. For example, if too much heat is applied then the properties of the metal can be hindered resulting in a weaker metal part. Signs that improper heating or cooling techniques were used include cracking next to the joint or discoloration on one side of the weld but not the other. Gases can also become trapped in the weld leading to porosity. Porosity is when gases like nitrogen, hydrogen, or oxygen released during the welding process freezes into the weld during the cooling process and form cavities in the weld. Signs that this occurred include holes in the metal. If this happens, the metal will crack or break, and it will result in a weaker metal. This is one of the most serious failures in the welding process because it can lead to a malfunction of the weld over time due to intense cracking overtime caused by weight being placed repeatedly and the weld failing.
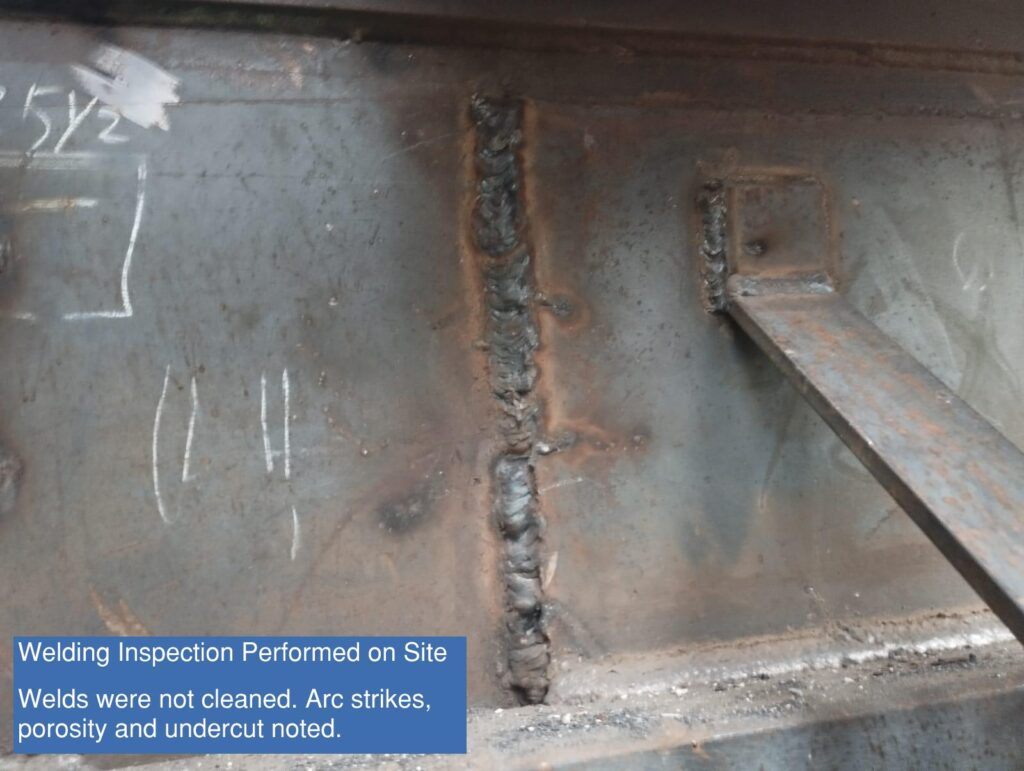

Third-party welding inspections are a requirement to guarantee that important welds have acceptable qualities that will ensure the length of life and structural integrity of any project. They’re meant to avoid any future failures that could result in loss of money for property owners or even disastrous events. Do you need a certified welding inspector? Do not hesitate to give us a call at (929)381-0030.